Case overview
In today’s rapidly evolving industrial landscape, the need for efficient and proactive maintenance strategies has become paramount. Predictive maintenance has emerged as a transformative approach, leveraging advanced data analytics and machine learning techniques to forecast equipment failures before they occur. This proactive methodology not only minimizes downtime but also optimizes operational efficiency and reduces maintenance costs.
Wavelet Analysis
Traditional methods like Fourier analysis are often limited in their ability to capture both frequency and time localization in the data. In order to avoid this problem Wavelet approach has been chosen. Wavelet analysis provides a way to decompose a time series into different frequency components at different scales, offering insights into both frequency content and temporal behavior simultaneously.

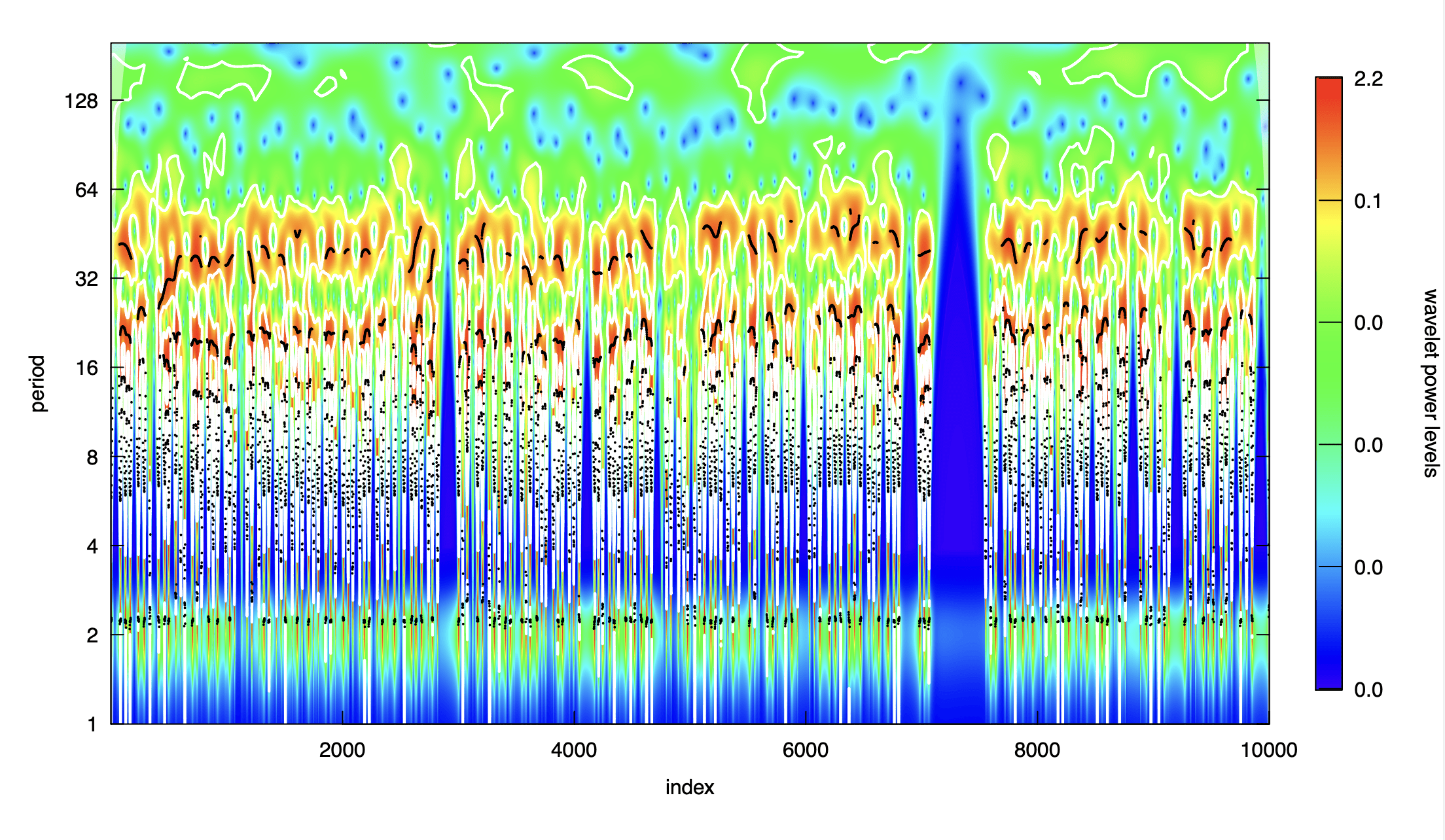
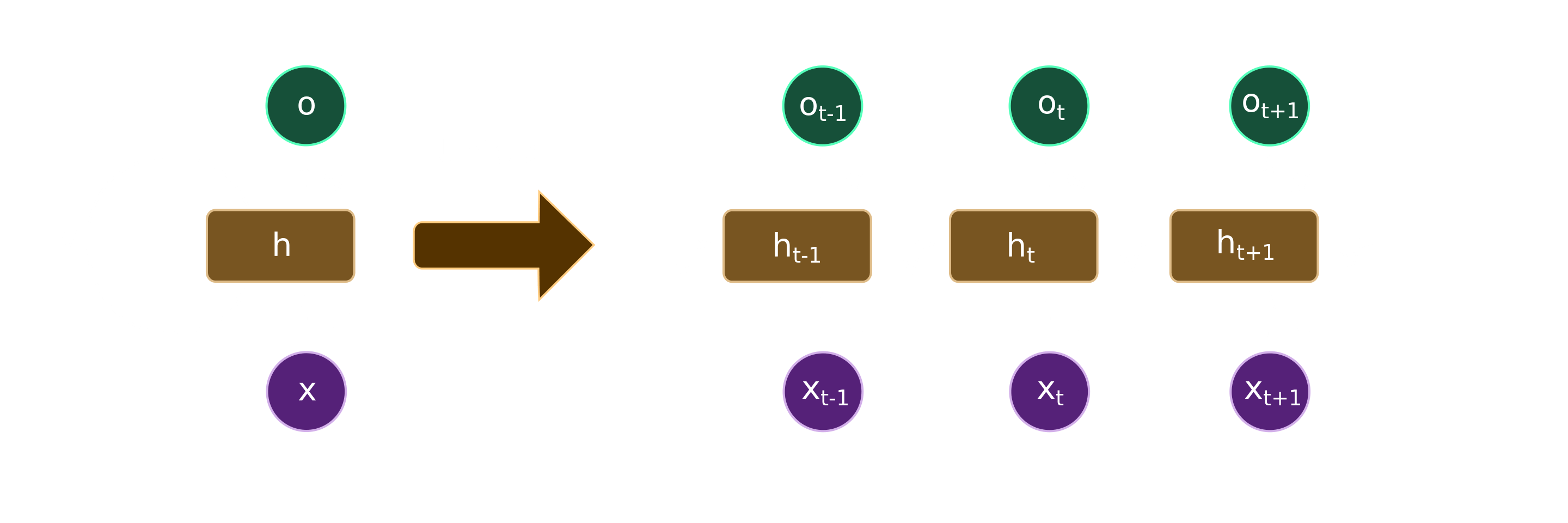
Neural Network
Results
In conclusion, the culmination of our predictive maintenance project marks a significant milestone in the evolution of industrial maintenance practices. Through meticulous research, robust data analysis, and innovative technology integration, we have successfully developed a sophisticated system of dashboards tailored to meet the dynamic needs of modern industrial operations.
Our system empowers stakeholders with real-time insights into the status of production lines, uptime metrics, and idle time trends. By harnessing the power of predictive analytics, we have enabled proactive maintenance interventions, thereby averting potential equipment failures and minimizing costly downtime.
Furthermore, our system goes beyond mere monitoring by incorporating advanced anomaly detection algorithms. These algorithms leverage historical data and machine learning models to identify subtle deviations in equipment behavior, thus alerting users to potential issues before they escalate into critical failures.
As we reflect on the journey that led us here, we recognize the collaborative efforts of multidisciplinary teams, the invaluable support of stakeholders, and the relentless pursuit of excellence. Moving forward, our predictive maintenance system stands poised to revolutionize the way industries approach asset reliability, operational efficiency, and overall productivity.
In closing, we extend our gratitude to all those who contributed to the success of this project. Together, we have laid the foundation for a future where downtime is minimized, resources are optimized, and industries thrive in an era of predictive maintenance excellence.


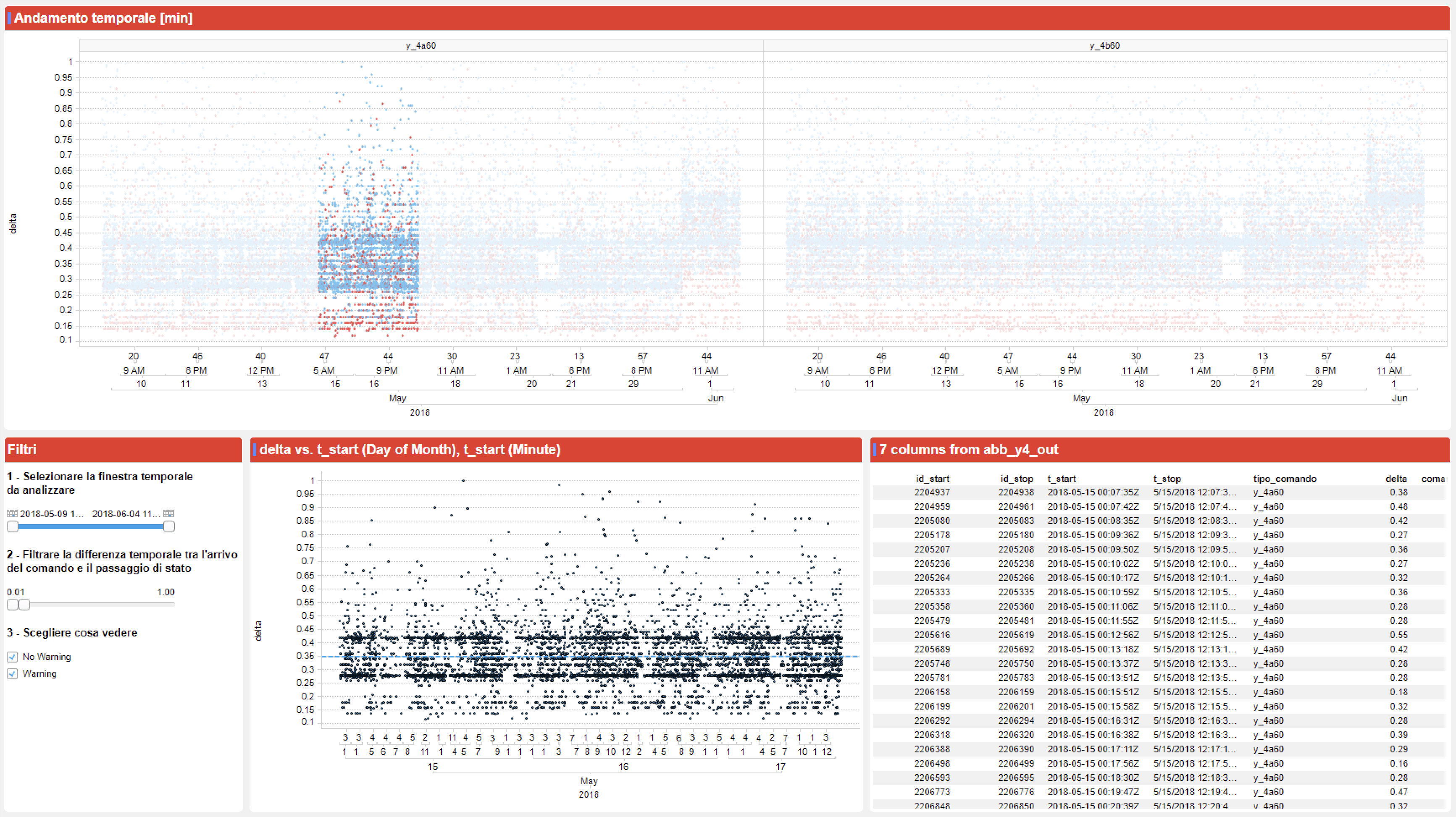