Case overview
The operator lacks efficient tools to assess the success of instrumentation recalibration, relying on manual comparison of new data with historical records. This process is labor-intensive and prone to errors, as historical data isn’t stored in a structured database format, requiring each comparison to involve data retrieval, cleaning, and manual graph creation.
Kiwi developed an AI model trained on historical data to automate the evaluation of new calibration results. This model analyzes each new calibration, comparing it with historical patterns and detecting anomalies. Based on this analysis, the AI model automatically determines whether the new calibration meets standards or if recalibration is necessary. If anomalies are detected, the system triggers an alert, providing details on the anomalies and recommending recalibration.
Feature Extraction
Feature extraction is the process of transforming raw data into a set of features that are more representative and informative for a particular task, such as classification, regression, or clustering. In the context of clustering, feature extraction plays a crucial role in identifying patterns and similarities in the data, which are then used to group similar data points into clusters.
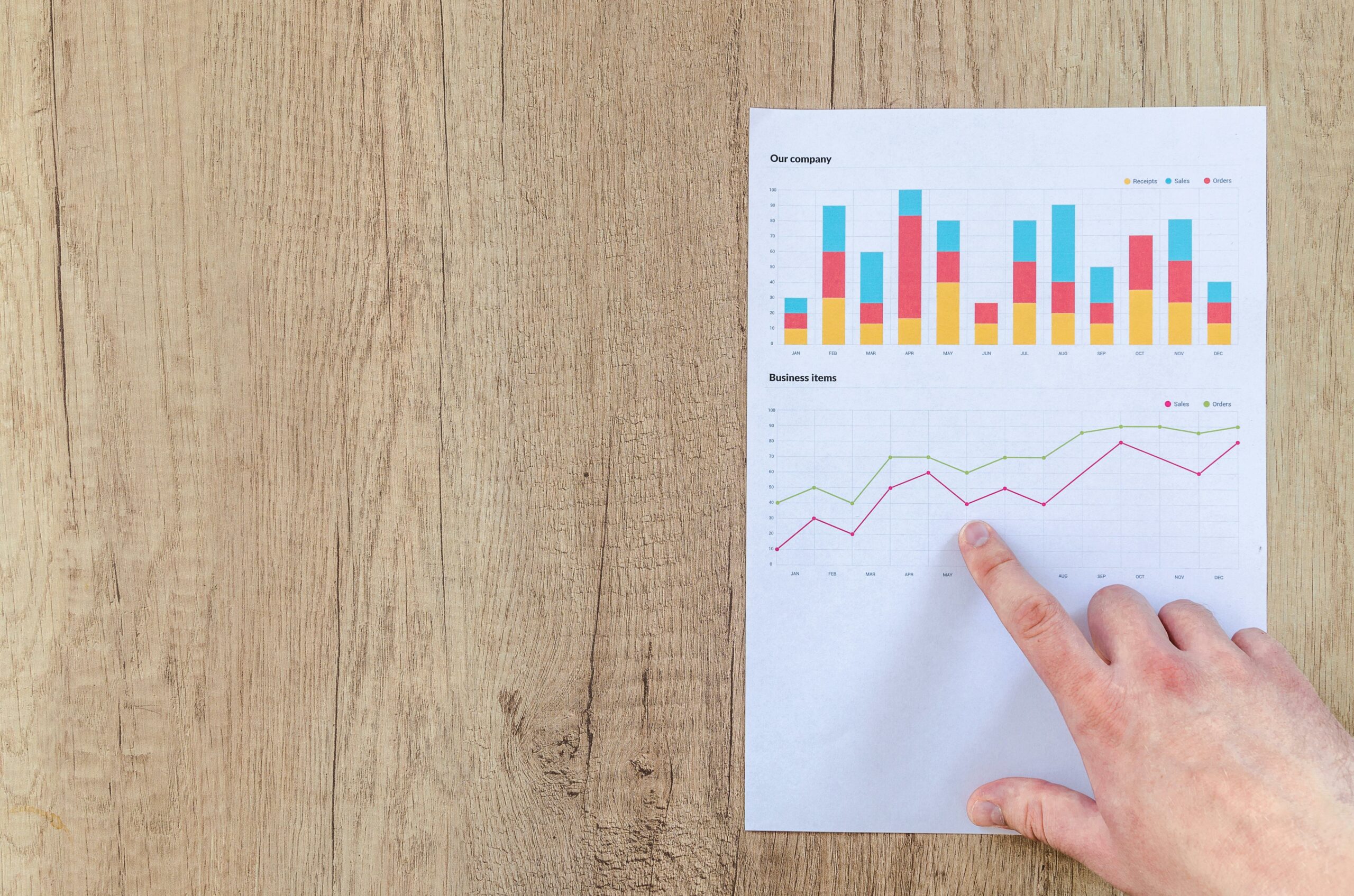
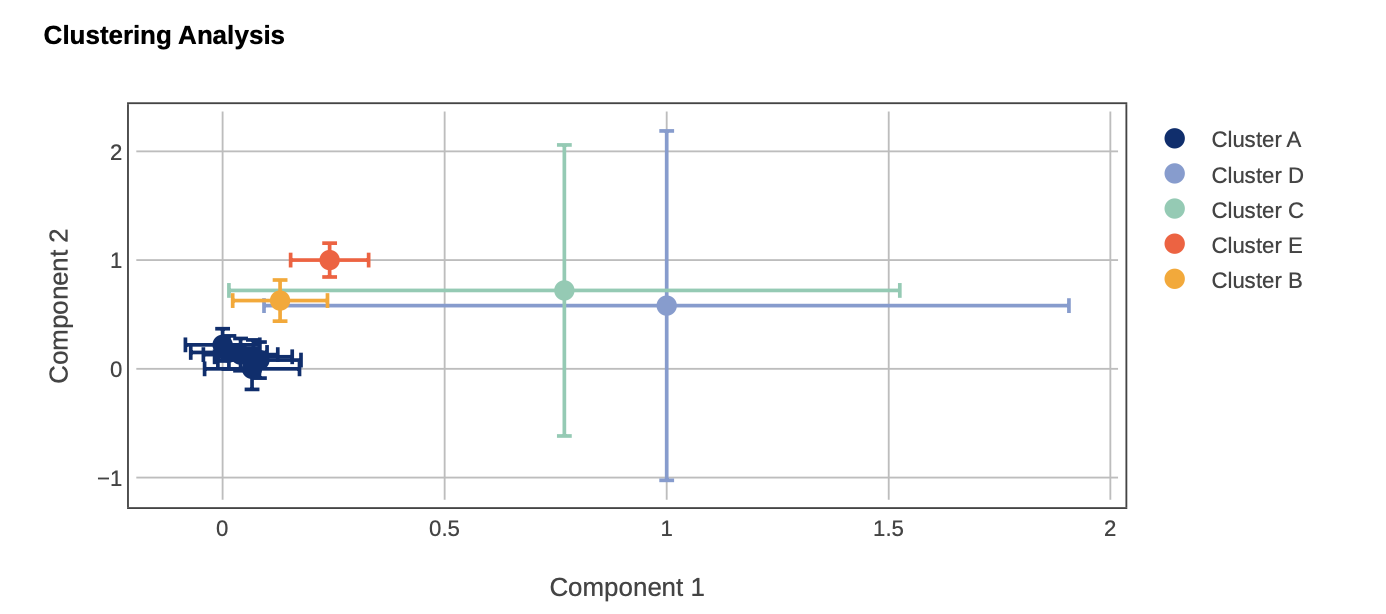
Cluster Analysis
Once the feature space is defined, clustering algorithms has been applied to group similar data points together. Common clustering algorithms include K-means, hierarchical clustering, DBSCAN, and Gaussian mixture models (GMM). These algorithms partition the data into clusters based on the similarity of data points in the feature space.
Results
Implementing the AI-driven decision support system for recalibration assessment yielded several significant benefits:
Improved Efficiency: By automating the evaluation process, the system dramatically reduced the time and effort required for recalibration assessment. Operators no longer need to manually retrieve, clean, and analyze historical data or create comparison graphs in Excel. This streamlined process allows operators to focus on other critical tasks, leading to increased productivity and operational efficiency.
Enhanced Accuracy: The AI model’s ability to analyze new calibration data against historical patterns significantly improves the accuracy of assessment. By leveraging machine learning algorithms trained on a large dataset of historical calibration results, the system can identify subtle anomalies that may not be immediately apparent to human operators. This results in more reliable evaluations and reduces the risk of overlooking calibration issues that could impact measurement accuracy.
Timely Intervention: The automatic triggering of alerts when anomalies are detected ensures that operators are promptly notified of potential calibration issues. This enables timely intervention and corrective action, minimizing the risk of inaccurate measurements or equipment malfunction. By proactively addressing calibration discrepancies, the system helps maintain the integrity and reliability of instrumentation data.
Data-Driven Decision Making: The AI model provides operators with actionable insights based on data analysis, empowering them to make informed decisions regarding recalibration. The system’s ability to identify specific anomalies and recommend recalibration when necessary helps operators prioritize maintenance tasks and allocate resources effectively. This data-driven approach to decision-making enhances overall operational effectiveness and ensures that instrumentation remains in optimal working condition.
Continuous Improvement: As the AI model continues to analyze new calibration data over time, it can adapt and improve its performance through iterative learning. By incorporating feedback from real-world calibration outcomes, the system can refine its algorithms and detection capabilities, further enhancing its accuracy and effectiveness. This continuous improvement cycle ensures that the decision support system remains robust and responsive to evolving calibration requirements.
In summary, the implementation of the AI-driven decision support system for recalibration assessment has led to significant efficiency gains, improved accuracy, timely intervention, data-driven decision-making, and ongoing performance enhancement. These results contribute to the overall reliability and effectiveness of instrumentation calibration processes, ultimately supporting the achievement of operational excellence and quality assurance goals.